Gas ballast: higher ultimate pressure, longer service life
Almost every oil-sealed vacuum pump designed for operation against atmospheric pressure is equipped with a gas ballast device. But what is the purpose of the gas ballast? Doesn't it increase the achievable ultimate pressure? And doesn't the vacuum pump take longer for evacuation as well?
Some of the various applications of the gas ballast will be presented in this short article.
The gas ballast:
The gas ballast on an oil-sealed vacuum pump dates back to an invention by Prof. Wolfgang Gaede from 1935 (Single or multi-stage vacuum pump for the conveyance of vapors and gas/vapor mixtures in order to generate low pressures). The original intention was to prevent the condensation of pumped gas vapors during the compression phase in the vacuum pump. But the gas ballast can do much more!
Structure and function:
The gas ballast is a device on oil-sealed vacuum pumps that introduces gas through a defined leak during the compression phase. The intake opening is usually located near the exhaust valves. The amount of gas ballast can vary through different options or be adjusted with a throttle valve. Typically, the amount of gas introduced via the gas ballast is about 10% of the nominal pumping capacity of the vacuum pump.
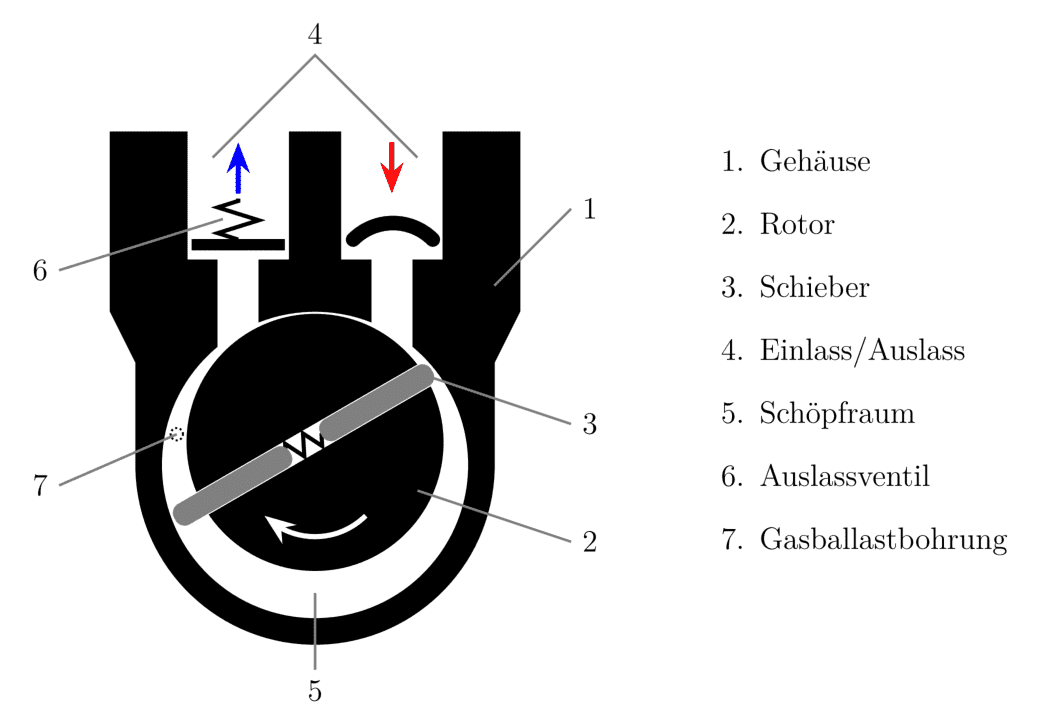
Figure 1: Rotary vane pump with gas ballast port
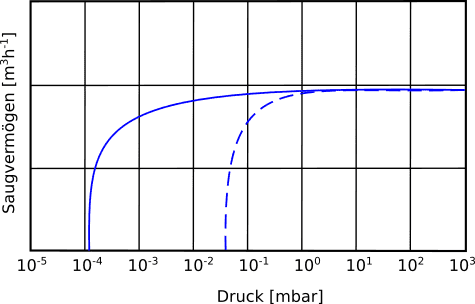
Figure 2: Pumping capacity with and without gas ballast (dashed line)
Possible applications for gas ballast:
1) Warming up the vacuum pump
Oil-sealed vacuum pumps require a certain operating temperature to efficiently convey gases with condensable vapor components without self-contamination. In many vacuum systems, the gas ballast on the vacuum pumps is therefore opened immediately after switching on. Even if there is no evacuation of the vacuum chamber, the vacuum pump must compress the gas entering through the gas ballast port, which warms up the pump through this compression work. Vacuum pumps reach the required operating temperature faster with gas ballast.
2) Conveyance of condensable vapors (using the example of water vapor)
Water vapor is one of the most common gases that vacuum pumps need to convey, partly due to process requirements, and partly because water vapor is one of the last gases to be released into the vacuum through desorption from surfaces.
Consider a typical oil-sealed vacuum pump with an operating temperature of approximately 80°C and a water vapor tolerance of 10 mbar (specified in the pump's datasheet). The required exhaust pressure to expel the conveyed gases is 1100 mbar absolute.
- Operation without gas ballast
First, let's consider what happens with a suction pressure of 10 mbar of pure water vapor without gas ballast. In the vacuum pump, the water vapor is compressed until the saturation vapor pressure of about psat,80°C=475 mbar is reached. After that, there is no further increase in pressure because the water vapor condenses and remains as liquid in the oil. The consequences are a significantly worse ultimate pressure of the vacuum pump, increased wear due to reduced lubricating properties, and increased pump corrosion due to the water content in the vacuum pump oil.
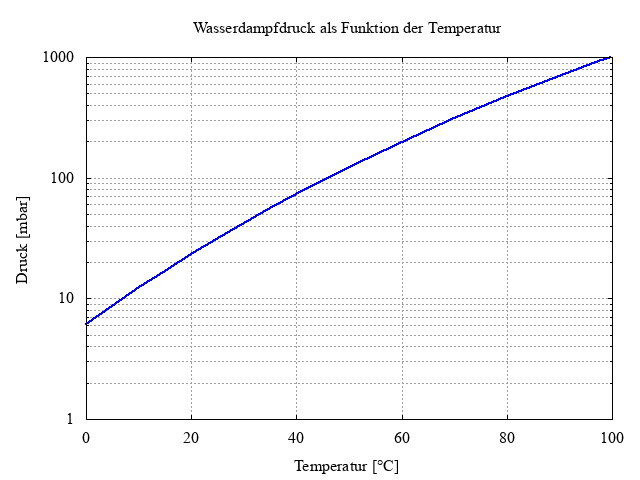
Figure 3: Water vapor pressure as a function of surface temperature
- Operation with gas ballast
With a standard gas ballast size, approximately 10% of the nominal pumping capacity flows through the gas ballast port. To simplify, let's assume that the pump's suction pressure is now also 10% of atmospheric pressure, i.e., psuction = 100 mbar. Of this, 10 mbar is pure water vapor, and a maximum of an additional 3 mbar is water vapor from the atmosphere. So, the vacuum pump contains 13 mbar of water vapor and 87 mbar of non-condensable gases.
These 100 mbar initial pressure must be compressed by a factor of 11 to reach the exhaust pressure of 1100 mbar. The water vapor partial pressure then becomes 143 mbar (13 mbar initial water vapor pressure multiplied by the compression factor of 11). This partial pressure is significantly below the saturation vapor pressure, meaning there is no condensation of water in the vacuum pump, and the vapors are expelled at the exhaust.
CAUTION!
The saturation vapor pressure is temperature-dependent. Immediately after starting the vacuum pump, it has a temperature of about 20°C, corresponding to a water vapor saturation vapor pressure of about psat,20°C=24mbar. Hence, cold vacuum pumps cannot convey water vapor!
3) Drying the vacuum pump between process phases or before shutdown
In many application processes, gas ballast cannot be used because it would cause the system pressure to increase too much. This may lead to contamination of the vacuum pump oil with condensate, such as water vapor in our example. The oil absorbs moisture.
Now, when the gas ballast is opened during process pauses or before shutting down the vacuum pumps in standby mode (i.e., no evacuation of the vacuum chamber), the following occurs. The low pressure created in the vacuum pump causes the condensed water to evaporate from the oil. Then, it is enriched with air from the outside (see point 2) and compressed again. The water vapor cannot recondense and is expelled at the exhaust of the vacuum pump. However, this process needs to run for some time to ensure that all the oil is dried.
4) Dilution of hazardous gases in the exhaust area
Coating processes are sometimes run reactively, where pure oxygen (O2) is added as a reaction gas. In the vacuum pump, this oxygen is compressed to about 1100 mbar at 80°C, significantly accelerating the carbonization of the vacuum pump oil.
To remedy this, the concentration of oxygen can be significantly reduced via the gas ballast by supplying inert gas, thus noticeably reducing the strain on the oil.
In addition to oxygen (O2), various other gases, some corrosive, explosive, or toxic, may also be used, which could potentially be neutralized by adding an appropriate gas ballast gas.
Conclusion
Correctly utilized, the gas ballast on an oil-sealed vacuum pump is an excellent tool for extending service life or protecting the vacuum pump. The disadvantage of the higher ultimate pressure is more than compensated for by the advantages of its use in general, especially since many processes operate cyclically and thus allow for the use of gas ballast at specific times.